Why Stainless Steel Processing So Difficult ?
- SG Prototype Team
- Jan 3, 2018
- 3 min read
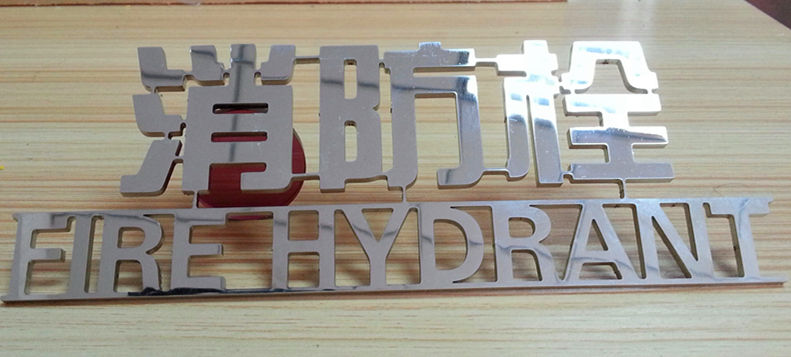
Stainless steel is difficult to process in prototyping mainly because of poor thermal conductivity of stainless steel, heat chips easily form tip edge debris, which is the main reason leading to blade damage. In addition, the processing of cutting power, high cutting temperature also brings some difficulties to the processing, cutting is often difficult to achieve satisfactory results.

There are some cutting tips in SG Prototype with stainless steel by our engineers.
Cut off the bar below φ40mm generally use high-speed steel cutting knife, you can achieve better cutting results. When machining a workpiece of φ40mm or larger, a carbide cutter can be used for improving the efficiency due to the lower cutting speed of the stainless steel.
1, The cutting edge of the tool must be 0 °, the conditions can be grinded on the tool grinder, this is the most important point. Because the stainless steel cut off, the friction between the chip and the groove wall is serious. If the chip can not be unrolled vertically, the crumbing phenomenon will occur and the knife will be hit severely. When the inclination of the blade is large, the effect of the chip scraping is not satisfactory.

2, The tip radius should not be too large, too large when the Vice Vice tool easy to wear. It may be because the arc at the chip thickness thinning, easy to produce work hardening, exacerbate the wear side of the tool.

3, Tool wear and tear should be timely grinding, stainless steel cutting knife sharpening standards, not only according to the main back to be set, but also pay special attention to the degree of wear behind the vice. If the vice behind the wear is too large, the friction between the tool and the groove side increases, resulting in narrow groove width, so that the chip is not easy to discharge, and tool wear and tear faster.
4, The front surface roughness of the tool should be minimized. Low surface roughness, can reduce the bonding wear and tear, reducing cutting force, cutting light, the practice proved that the tool after grinding than before the life of the tool significantly improved.
5, The edge grinding out about 0.2mm negative chamfering, can reduce the chipping phenomenon grinding, better edge quality. The lower part of the knife body is used to increase the rigidity. The vice angle of the cutter is grinded by the grinding wheel cylindrical, the rigidity is better, and the actual relief angle is about 2 ° ~ 3 °.
Stainless steel cutting tool materials generally choose not easy to bond with the wear and tear of the YG alloy, I chose the better strength YG8, knife width according to the choice of bar diameter, cutting speed of about 60m / min.
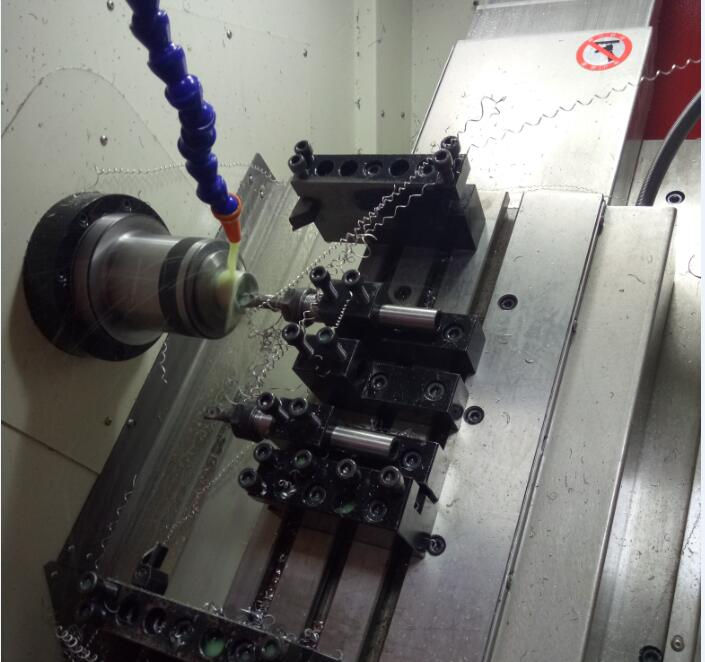
This tool can meet the needs of general processing, φ40 ~ φ80MM bar feed can be cut off once, no need to rush knife. Processing should pay attention to the stainless steel chip is very sharp, such as the chip is too long, the feed to retreat, so that cut off the chip, so as to avoid danger, the tool does not stop when the retraction of the workpiece surface to reduce work hardening. Cut off the solid workpiece, in order to avoid the tool crushing, cut into the center can leave about 1 ~ 2mm hand bend off.
6, For cutting stainless steel, under normal circumstances, wet cut than dry cutting tool to be several times longer. And depends on the speed and cutting knife, speed is not high water, cut the knife out of the red immediately.
