Sandblasting tips and tricks
- SG Prototype Team
- Jul 15, 2018
- 2 min read

Sandblasting(Abrasive Blasting) process: which uses compressed gas to spray the sand at high speed and pressure (commonly sprayed with copper ore, quartz sand, corundum, iron sand, Hainan sand, etc.) to the surface of the workpiece. Under the action of the impact of the spray on the surface of the workpiece and the cutting, the surface is given a certain degree of cleanliness (such as rust removal), and at the same time, the fatigue resistance of the workpiece is also improved; the sandblasting treatment causes the surface to form. A certain roughness increases the adhesion between it and the coating, prolongs the durability of the coating, and also facilitates the smoothing and decoration of the coating.
Applicable material
Metal, plastic and glass are mostly surface treated in rapid prototyping.
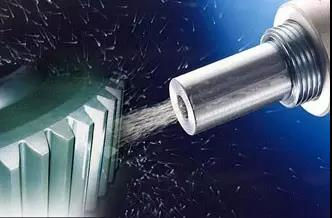
Design considerations
1. Common abrasives are steel sand, alumina, quartz sand, silicon carbide, etc., but the most used in China is quartz sand.
2. Sand blasting is an efficient process for removing surface oil (de-oiling) and rust removal. Different sand materials also bring different texture effects.
3. Before batch blasting, a large amount of preparation is required in advance, such as selecting the appropriate abrasive according to the material characteristics of the workpiece; adjusting the appropriate spray speed, pressure, distance, and performing multiple test spray sampling.
4. The blasting process is efficient and the processing quality is good.
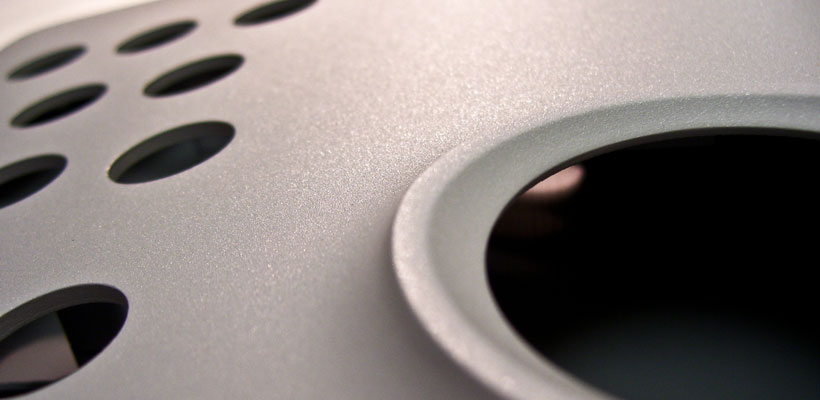
Process cost
No mold costs. However, it may be necessary to cover the protective layer, the cost being determined by the surface area of the workpiece.
The labor cost is medium, because the quality of sandblasting depends on manual pre-treatment work.
Environmental impact
The sandblasting process will cause dust pollution, and the staff should be protected from upper body and respiratory protection.
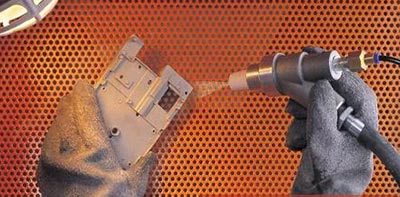
Process characteristics: The production operation at room temperature and the formation of the plating layer are not electrodeposition. The rotation of the plated parts of the loading parts causes the parts of the cylinders to collide with each other and realize the transfer of the mechanical industry to form a plating layer.
Process flow:
Pre-treatment, degreasing, descaling (under-line treatment)→washing→flash plating replacement copper→water washing→mechanical galvanizing deposition transition bottom layer→mechanical galvanizing deposition→water polishing→part-out separation→hot water washing (or press Requires surface passivation of the part, immersion related protective layer) → dry and dry → inspection acceptance.
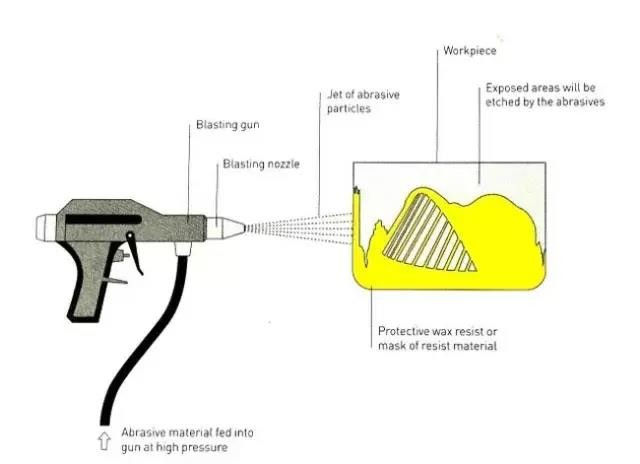
1. Protective equipment must be worn before work, and it is not allowed to work with naked arms. No less than two people at work.
2. The compressed air valve should be opened slowly, and the air pressure must not exceed 0.8 MPa.
3, sandblasting particle size should be compatible with the work requirements, generally between 10 to 20, the sand should be kept dry.
4. When the sand blasting machine is working, it is forbidden for the unrelated personnel to approach. When cleaning and adjusting the operating part, stop it.
5. After the work, the ventilation and dust removal equipment should continue to operate for five minutes and then shut down to discharge indoor dust and keep the site clean.
Example: Other related products (multiple pictures)
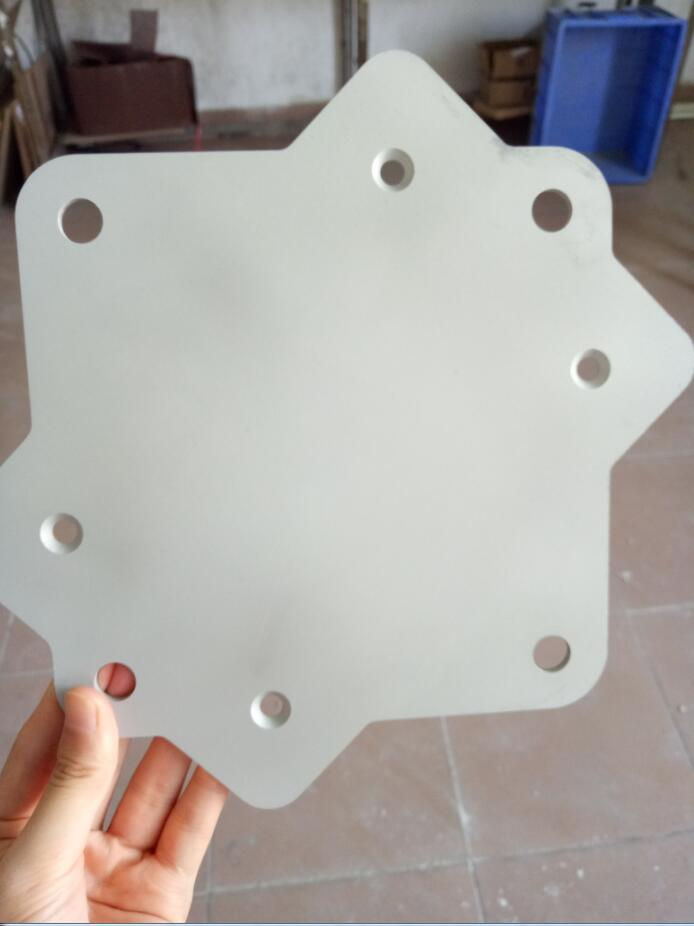



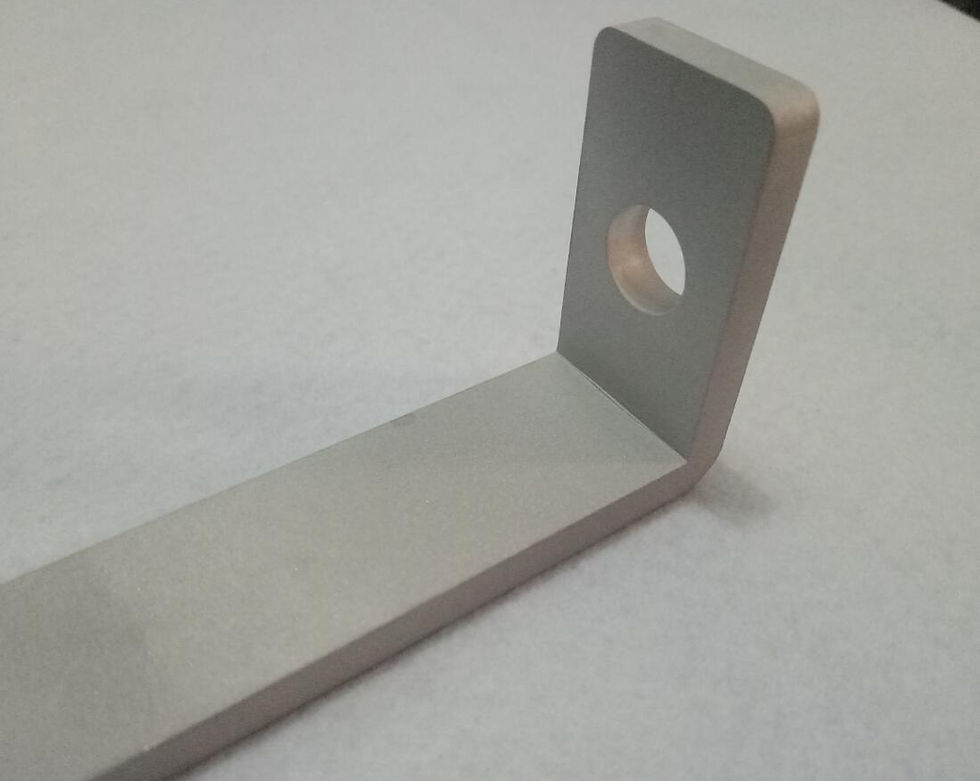
Comments